Behind the innovations: Meltio
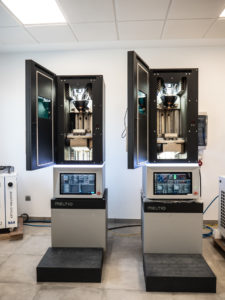
AMM – What was the motivation to start developing Meltio’s multi-laser head?
Carlos Capel, Product Manager at Meltio – Before each development, a need is always detected, so at Meltio, a joint venture between Sicnova and Additec, we saw that there was a great opportunity to give industry the ability to manufacture metal parts at low cost.
That was our main motivation, to provide our current and future customers with a totally disruptive manufacturing solution, and at the same time complementary to traditional manufacturing processes.
This provides a wide range of possibilities and manufacturing materials where conventional production models do not reach.
AMM – Can you tell us about the product development process? Any anecdotes or obstacles that got in the way?
Meltio – The process has not been easy or quick, it has been an intense work by all the departments that make up the company, from R+D+I, through the operations department, marketing, quality, etc… to get to where we are today.
There have been many stones along the way, but perhaps the biggest one was the pandemic caused by COVID-19. It appeared a few months after the creation of the company and coincided with the moment when the product was launched on the market. The industry and the market came to a standstill in much of the world, but we used this crisis as an opportunity to focus on product development, testing and validation of the equipment. Meltio has achieved a reliable and versatile product in record time.
AMM- What is the technology behind this innovation?
Meltio – Meltio’s Laser Metal Deposition (LMD) technology is used in the print head of its 3D printers and its integration with robot and CNC. It consists of six lasers that concentrate energy on a single point. This melts the metal wire in a way that enables direct metal additive manufacturing, part repair, parameterised coatings, autogenous welding and even texturing of parts to optimise efficiency depending on the application.
These solutions are constantly being developed and updated to become more and more versatile in terms of material portfolio, speed, final part resolution and manufacturing cost optimisation.
AMM – What are the main advantages offered by this innovative product, what needs does it cover and how can it improve the life of companies?
Meltio – The equipment offers multiple advantages. One of the most attractive to customers is often the possibility of manufacturing parts with 99.998% density. This is the quality of the technology that stands out most in the aeronautical and automotive industries, as the isotropic properties of the part are exactly the same as those produced with subtractive manufacturing. In addition, it offers the added value of being able to manufacture practically any geometry. Another of the technology’s strengths is its cost, as Meltio’s equipment has a considerably low price compared to other metal additive manufacturing technologies.
Meltio meets many of our customers’ needs. It manufactures final parts, specialised and customised tooling, provides solutions in industrial maintenance departments, and an infinite number of solutions and developments that our customers are discovering day by day. This technology is capable of extending the life of many pieces of equipment that become obsolete and repairing previously manufactured parts with the addition of parameterised material in specific areas of the part, repairing or strengthening parts to maintain production or further extend their production time.
AMM – What industries is the innovation mainly aimed at?
Meltio – Meltio has a place in a wide range of industries. Our customers come from the aeronautics, defence, automotive and industrial maintenance sectors, among others. This is such an innovative development that we are sometimes unaware of the capabilities of the technology itself, as it brings a myriad of possibilities that make it useful in any industry.
AMM – What are the main obstacles faced by a company that wants to develop an innovative product?
Meltio – Companies that innovate sometimes encounter people’s reluctance to change the way they work. However, Meltio is a clean, safe technology with virtually unlimited manufacturing capabilities. Gradually, new generations are looking for this leap in efficiency, both in terms of costs and sustainability, and to reduce emissions and energy consumption compared to other manufacturing methods. Innovative companies with new production methods are becoming more efficient as they are able to tackle new projects that they would not be able to manufacture in any other way.
Stay informed
Advanced Manufacturing Madrid successfully closes its 16th edition, with more than 13,500 attendees
With 625 exhibiting companies, the fair registered 58,424 commercial interactions during the two days of the event. The Tech Congress 4.0, the expansion of the
Winners of the 3rd Advanced Manufacturing Awards: recognising excellence and innovation in industry
Eurecat, Industrias Alegre, Aldakin, ABB, MESBook, Escuela de Hostelería de Leioa and HRE Hidraulic have been awarded in the seven categories of this edition. The
Talent crisis: over 60% of industry can’t find skilled labour
The latest study conducted by Easyfairs, organizer of the leading industrial sector fair Advanced Manufacturing, has revealed that the biggest challenge for 60.2% of companies
3rd Advanced Manufacturing Awards unveils its finalists
The awards organized by the Advanced Manufacturing Madrid trade show recognize the most innovative, efficient, and sustainable projects in the Spanish industrial sector. This year,