Innovative fasteners for a sustainable future, for the latest applications and for the sectors of the future
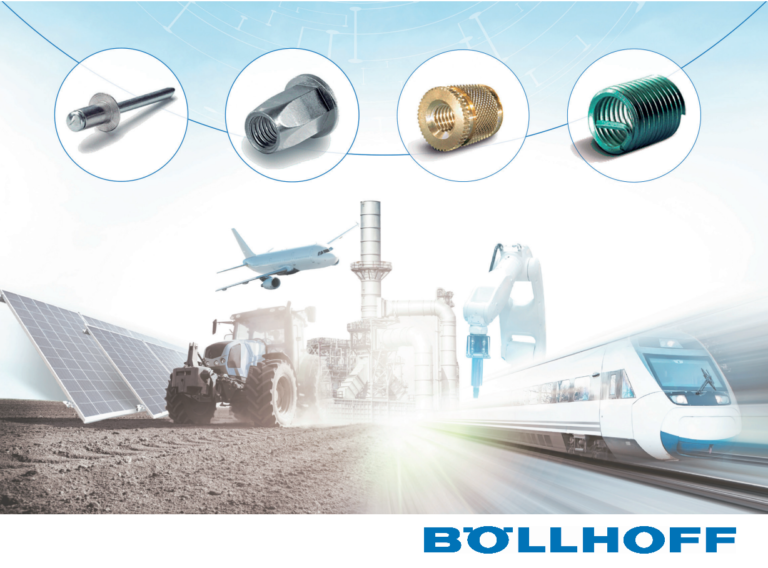
The Böllhoff Group (Hall 8, Stand 8C21) is a world leader in the manufacture and supply of 360° fastening technologies, installation equipment and logistics solutions. As a family-owned company in its fourth generation, it has always taken long-term decisions, being aware of the effects of its actions on future generations, which is why adopting a sustainable approach and acting responsibly are firmly rooted in its corporate values.
Böllhoff is synonymous with long-term success thanks to its innovative capacity and local presence since 1877. Its customer orientation enables it to understand the specific fastening needs of all sectors of industry, working alongside the customer from the design phase through to production – for successful fastenings every time.
360° products and services
The Böllhoff range extends from standard fasteners according to DIN and ISO specifications to special fasteners such as HELICOIL® threaded inserts or equipment for the installation of various types of fasteners. This product offering, which will be on display at Stand 8C21 in Hall 8 at MetalMadrid, is rounded off by a wide range of services related to fastening technologies, such as tests in its own accredited laboratory, application-specific advice and the cost-effective supply of fasteners.
Böllhoff works to create fasteners for a sustainable future.
Its products and services are used in numerous industries, where they contribute to conserving resources and reducing CO2 emissions.
Current trends, such as electric mobility and lightweight structures, require appropriate fastening technology solutions. Böllhoff products are already helping to reduce weight and emissions in many sectors and to create strong and stable connections for future industries such as renewable energy generation.
Innovative products and processes
Creation of elastic threads in thin sheet metal for the fastening of photovoltaic modules with RIVKLE® blind rivet nuts.
RIVKLE® blind rivet nuts provide a reliable and strong thread in thin components where tapping is not possible. The wide variety of types and dimensions means that there is the perfect solution for every application, whether in sheet metal or plastics.
RIVKLE® Seal Ring blind rivet nuts for the creation of watertight, load-bearing threads in battery trays for electric cars.
The RIVKLE® Seal Ring technology protects the joints from external aggressions, while guaranteeing the tightness to any kind of liquid and maintaining the performance level of the metal joints (metal-to-metal contact) in the long term. This is made possible by a gasket that is securely attached to the RIVKLE® rivet nut, which remains securely in place under all circumstances, even during automatic installation by means of blown-in feed. The sealing is in accordance with ISO 20653, specifications IPX7; resistant to UV, temperatures up to 220°C and all types of fluids (oils, hydrocarbons, etc.).
HELICOIL® thread inserts are used for the reinforcement of threads in wind turbines such as generators.
This technology, which has proven itself in practice for more than 65 years, enables high-strength joints in soft metals with reduced shear strength.
They are available in the HELICOIL® Free Running version and in the HELICOIL® Screwlock version with screw locking.
RIVCLINCH® clamping for the robust connection of sheet metal and profiles without the need for material input in ventilation ducts, battery trays of electric cars or the walls of wind turbine nacelles.
RIVCLINCH® is used to join sheets and profiles by cold deformation of the material. The result is the joining of two or more sheets through a clinching point which is produced by the interaction of a punch and a die. In addition to steel and stainless steel materials, clinching can also be used to join aluminium and other materials in a rational and environmentally friendly way, as there are no chips, no heat distortion of the joining area and therefore no fumes, and low energy consumption. Furthermore, surface-treated sheets can also be joined by clinching without any damage or deterioration.
ONSERT® adhesive bonding system for fixing parts to lightweight structures
ONSERT® is the perfect fixing solution when welding is not possible. Fasteners with a transparent plastic base are bonded to the customer’s component using a light-curing adhesive.
The outstanding features of this adhesive bonding system are short cycle times, no damage or marking of the material and flexibility in terms of the fasteners and the method that can be used.
HUCK® structural and collar rivets are used for high-strength connections in solar panel structures.
The HUCK® range is specifically designed and manufactured for use in applications where high strength and safety is a key factor, creating a high quality, maintenance-free joint with a long life cycle. These fasteners have high tensile strength, shear strength and vibration resistance. They are a good alternative to welding and a more efficient fastening system than the use of nuts and bolts.
Implementation of high-strength threads in plastic plugs for electric vehicle charging by incorporating AMTEC® threaded inserts.
AMTEC® stands for “After Moulding TEChnology” and refers to the insertion of metal inserts into plastic parts after moulding. With these inserts, threads can be created securely and with almost no stress on plastic parts.
Nowadays, plastics are indispensable in the manufacture of lightweight structures, as they are used in an increasing number of applications. The great flexibility in the processing and design of components made of this material means that metallic materials are increasingly being replaced by plastics. On the other hand, thanks to their excellent mechanical properties, low weight and lower manufacturing costs, plastics are a key element of today’s industry. With AMTEC® metal inserts, an advantageous synergy effect is achieved by combining high-strength metals with plastics.
Böllhoff’s RIVSET® self-pierce rivets and RIVTAC® high-speed nails are used to create strong multi-layer and hybrid connections in modern lightweight car bodies.
The RIVSET® self-piercing rivet is a fastening system that creates mechanically strong, high-strength joints in similar or dissimilar materials and even joints with more than two layers without the need for pre-drilling, emissions and noise.
Focusing on the optimisation potential of fastening technologies and taking sustainability to the next level
Sustainability is often associated with terms such as “durable”, “environmentally friendly”, “resource efficient” and “reusable”. All these properties also apply unreservedly to one of the most commonly used fasteners: the screw.
Screws can be manufactured very cost-effectively using the cold-forming process. This requires very little energy in the manufacturing process, while hardly any raw material is lost.
Provided the joint has been designed correctly, a bolt can be loosened and reused without any problem. This means that an assembly that has been assembled can be separated and professionally repaired or recycled. The screw itself can simply be returned to the material cycle once it reaches the end of its useful life. The basic properties of these tiny elements offer a lot of sustainability, while good fastener design has additional potential.
In practice, optimal fastener design has additional potential to improve sustainability. Often, however, the capabilities of fasteners are not exploited efficiently enough. One reason for this is that technological developments constantly place new demands on fastening technology, and designers cannot keep up with all of them. This is where our application technology consultancy service comes in.
Application-specific engineering advice
Böllhoff’s experienced team of technicians and engineers advises and assists its customers in designing joints as efficiently as possible and ultimately more sustainably. After all, functional optimisation often means that an equally strong connection can be achieved with fewer and smaller fasteners than before, thus using less material and fewer resources. In this way, the dimensions and weight of the components can also be reduced – an advantage for customers and the environment.
Come to Stand 8C21, Hall 8, at MetalMadrid and get a first-hand look at the Böllhoff 360° fastening technology range for industry and all its advantages.
Böllhoff Group
MetalMadrid – Stand 8C21, Hall 8.
More info at www.boellhoff.es
E-mail: info_es@boellhoff.com
Tel. +34 91 661 91 88
Stay informed
Advanced Manufacturing Madrid successfully closes its 16th edition, with more than 13,500 attendees
With 625 exhibiting companies, the fair registered 58,424 commercial interactions during the two days of the event. The Tech Congress 4.0, the expansion of the
Winners of the 3rd Advanced Manufacturing Awards: recognising excellence and innovation in industry
Eurecat, Industrias Alegre, Aldakin, ABB, MESBook, Escuela de Hostelería de Leioa and HRE Hidraulic have been awarded in the seven categories of this edition. The
Talent crisis: over 60% of industry can’t find skilled labour
The latest study conducted by Easyfairs, organizer of the leading industrial sector fair Advanced Manufacturing, has revealed that the biggest challenge for 60.2% of companies
3rd Advanced Manufacturing Awards unveils its finalists
The awards organized by the Advanced Manufacturing Madrid trade show recognize the most innovative, efficient, and sustainable projects in the Spanish industrial sector. This year,